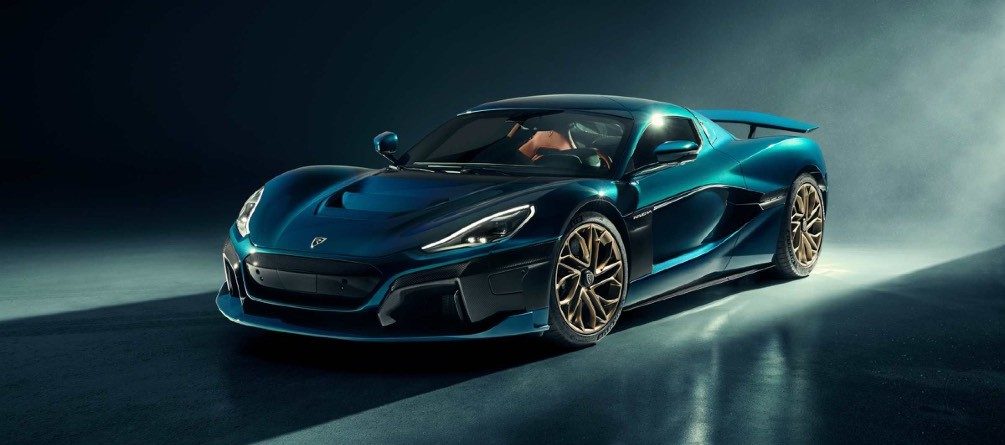
Bugatti-Rimac : การผสมผสานความเป็นเลิศด้านยานยนต์
รถยนต์ไฮเปอร์คาร์ถือเป็นสุดยอดของวิศวกรรมยานยนต์ที่เน้นความแม่นยำ คุณภาพ และการประนีประนอมเป็นหัวใจสำคัญของทุกชิ้นส่วน เพื่อให้เป็นไปตามมาตรฐานระดับสูงเหล่านี้ Bugatti-Rimac ได้รวม FreeScan Trak Pro2 ของ SHINING 3D เข้ากับห้องปฏิบัติการมาตรวิทยาที่ล้ำสมัย เพื่อให้มั่นใจถึงความแม่นยำที่ไร้ที่ติในกระบวนการควบคุมคุณภาพ
Bugatti-Rimac เป็นบริษัทร่วมทุนเชิงกลยุทธ์ระหว่างแบรนด์รถยนต์ระดับตำนานสองแบรนด์ ได้แก่ Bugatti Automobiles ซึ่งก่อตั้งมากว่า 110 ปี และ Rimac Automobili ซึ่งมีชื่อเสียงด้านความเป็นผู้นำด้านยานยนต์ไฟฟ้าสมรรถนะสูง (EV) บริษัทมีสำนักงานใหญ่ในเมือง Sveta Nedelja ภายใต้การนำของ Mate Rimac และมีแผนที่จะย้ายไปยัง Rimac Campus มูลค่า 200 ล้านยูโร ซึ่งเป็นโรงงานแห่งอนาคตสำหรับการผลิตไฮเปอร์คาร์และการพัฒนาเทคโนโลยี EV ขั้นสูง
- หัวใจหลักในการผลิตของ Rimac Automobili คือ Nevera ซึ่งเป็นไฮเปอร์คาร์ไฟฟ้าที่ก้าวล้ำหน้าพร้อมประสิทธิภาพที่ทำลายสถิติ โมโนค็อกที่ทำจากคาร์บอนไฟเบอร์ ซึ่งเป็นโมโนค็อกที่มีขนาดใหญ่ที่สุดเท่าที่มีมาในการผลิตแบบต่อเนื่อง ได้รับการควบคุมคุณภาพอย่างเข้มงวดเพื่อให้แน่ใจว่าแต่ละยูนิตเป็นไปตามข้อกำหนด การวัดที่แม่นยำช่วยรับประกันความพอดีที่สมบูรณ์แบบระหว่างยูนิตและส่วนประกอบที่ติดตั้ง เช่น ระบบกันสะเทือน เป็นต้น ผลงานชิ้นเอกด้านโครงสร้างและวิศวกรรมน้ำหนัก 200 กก. ที่ทำหน้าที่เป็นกระดูกสันหลังของรถยนต์เป็นชิ้นส่วนที่ใหญ่ที่สุดที่ต้องผ่านการตรวจสอบก่อนเริ่มการผลิต
“ที่ Rimac ความแม่นยำคือทุกสิ่ง ส่วนประกอบทุกชิ้นต้องเป็นไปตามมาตรฐานสูงสุดเพื่อรับประกันประสิทธิภาพและความปลอดภัย”
— Annamaria Hamata นักวิเคราะห์คุณภาพ
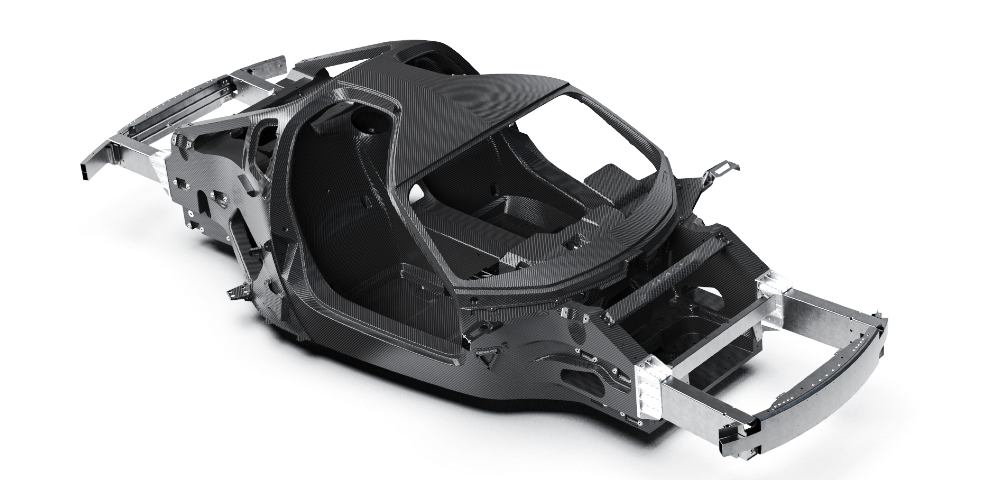
Inspection of High-End Hypercars Requires High-End 3D Digitizing Solutions : การตรวจสอบไฮเปอร์คาร์ระดับไฮเอนด์ต้องใช้โซลูชัน 3 มิติระดับไฮเอนด์ !!
- Bugatti-Rimac ใช้ขั้นตอนการตรวจสอบหลายขั้นตอน รวมถึงการสแกน 3 มิติ เพื่อรับประกันคุณภาพที่ไร้ที่ติในการผลิต หลังจากบูรณาการ FreeScan Trak Pro เป็นครั้งแรกในปี 2023 บริษัทได้อัปเกรดเป็น
FreeScan Trak Pro2 ซึ่งช่วยเพิ่มประสิทธิภาพและความแม่นยำในเวิร์กโฟลว์ที่ขับเคลื่อนด้วยการวัด
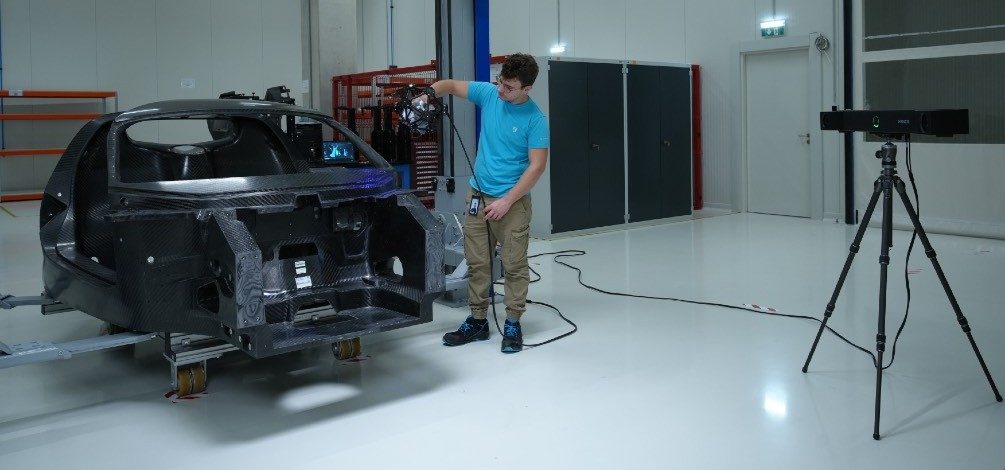
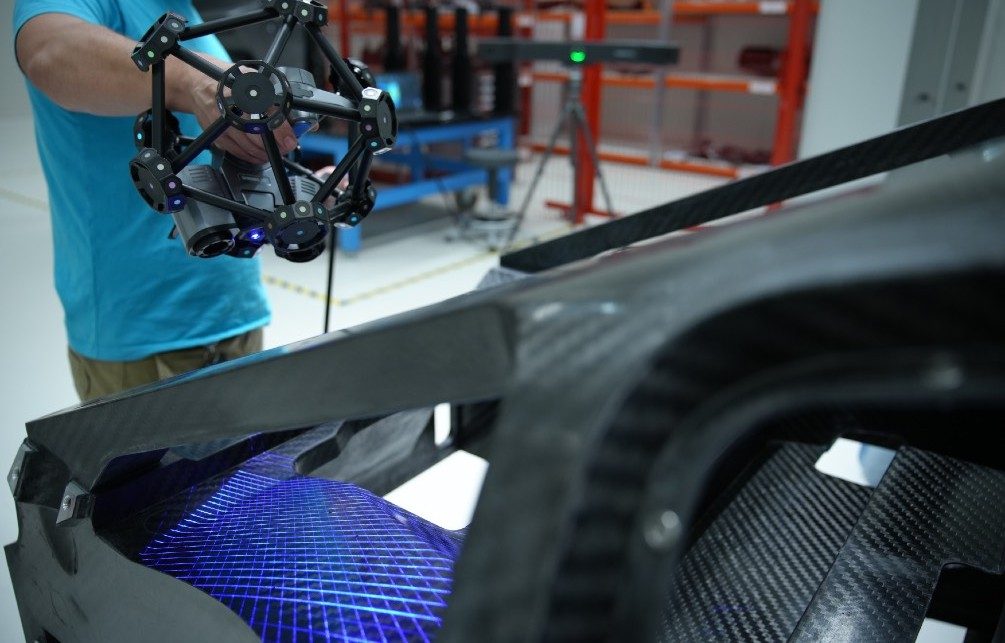
3D Scanning Operation of Nevera Monocoque in the Metrology Lab : ห้องปฏิบัติการมาตรวิทยา
- หนึ่งในองค์ประกอบที่สำคัญที่สุดที่ได้รับการตรวจสอบคือโมโนค็อกคาร์บอนไฟเบอร์ของ Nevera ซึ่งเป็นส่วนหลักของแชสซีและกระดูกสันหลังโดยแท้จริงของตัวรถทั้งหมด เป้าหมายคือการตรวจสอบคุณภาพการผลิตของโมโนค็อก จัดตำแหน่งให้ตรงกับส่วนประกอบคาร์บอนไฟเบอร์อื่นๆ และให้แน่ใจว่าจุดยึดสำหรับระบบกันสะเทือน ระบบส่งกำลัง และแชสซีอยู่ในตำแหน่งที่แม่นยำ ในกรณีนี้ จุดยึดบนแชสซี ด้านล่าง และคุณลักษณะสำคัญในห้องนักบินได้รับการสแกนโดยใช้ FreeScan Trak Pro2 ข้อได้เปรียบหลักของระบบคือความสามารถในการรวบรวมข้อมูลที่มีความแม่นยำสูงโดยไม่ต้องพ่นสแกนหรือวางมาร์กเกอร์จำนวนมาก
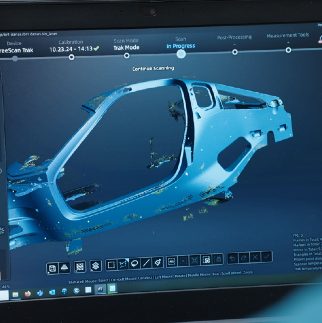
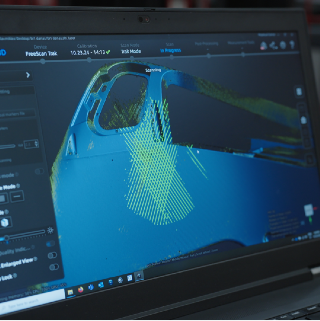
หลังจากการสแกน ข้อมูลจะถูกประมวลผลในซอฟต์แวร์ตรวจสอบ 3 มิติ ซึ่งวิศวกรจะตรวจสอบค่าความคลาดเคลื่อนตามข้อกำหนดการออกแบบ ด้วยห้องแล็บควบคุมคุณภาพที่บูรณาการเข้ากับโรงงานผลิต ทำให้สามารถระบุและแก้ไขความคลาดเคลื่อนในการผลิตที่อาจเกิดขึ้นได้อย่างรวดเร็ว ช่วยป้องกันความล่าช้าที่มีค่าใช้จ่ายสูง “FreeScan Trak Pro2 ช่วยให้เราตรวจสอบโครงสร้างคาร์บอนไฟเบอร์ที่ซับซ้อนได้รวดเร็วและแม่นยำยิ่งขึ้น…ด้วยข้อมูลแบบเรียลไทม์ เราจึงสามารถแก้ไขความเบี่ยงเบนใดๆ ได้ทันที จึงมั่นใจได้ว่าชิ้นส่วนทุกชิ้นจะพอดีอย่างสมบูรณ์แบบ”
— Ivan Radicevic ช่างเทคนิคควบคุมคุณภาพ
Credit : SHININD3D
-
InfraredLaserWireless
Creality CR-Raptor สแกนสามมิติ Wireless NIR | Parallel Laser 7
Price range: 12,900.00 ฿ through 39,900.00 ฿ Select options This product has multiple variants. The options may be chosen on the product page -
InfraredLaserWireless
Creality Raptor Pro สแกนสามมิติ Wireless NIR | Parallel Laser 7 | Cross Laser 22
Price range: 12,900.00 ฿ through 69,900.00 ฿ Select options This product has multiple variants. The options may be chosen on the product page -
HotInfraredLaserWireless
Creality Raptor X สแกนสามมิติ Wireless NIR | Parallel Laser 7 | Cross Laser 34
Price range: 12,900.00 ฿ through 129,000.00 ฿ Select options This product has multiple variants. The options may be chosen on the product page -
HotLaserLEDHandheld Scan
EinScan HX2 – 3D Scanner Hybrid Blue Laser & Blue LED
Original price was: 469,000.00 ฿.359,000.00 ฿Current price is: 359,000.00 ฿. Add to cart -
HotInfraredLaserLEDHandheld Scan
FreeScan Combo – 3D Scanner Hybrid Light Source and Multifunctional
โปรดสอบถามราคา Read more